Chewy v. U.S. Department of Labor: Undermining OSHA’s Regulatory Regime
In Chewy v. U.S. Department of Labor, 69 F.4th 773 (11th Cir. May 30, 2023), an Eleventh Circuit panel reversed the Occupational Safety & Health Administration’s (“OSHA”) imposition of a penalty upon an employer under the general obligation to ensure worker safety. The case involved the use of forklifts in proximity to shelving. In such circumstances forklifts can go underneath shelving and pin the operator to a cross beam, causing serious injury. Such events, forklifts going under shelving, are commonly referred to in the trade as “underrides.”[1]
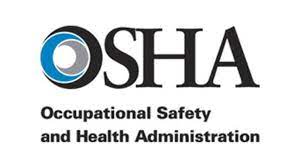
In May 2019, OSHA issued a citation and notification of penalty to Chewy after one worker had been severely injured in an underride accident, and a second had been killed several months later. In response to the first accident, Chewy modified its training regimen regarding the risk of underrides, but did not lower itself shelving to prevent such occurrences.
Chewy challenged the citation on the basis of an OSHA regulation that mandated training of forklift operators, including training regarding the risk posed by underrides. Chewy asserted that to satisfy its OSHA obligations it merely need train workers regarding the risk of underrides. In its view, the training obligation preempted any further duty suggested by the general worker safety standard, such as altering physical aspects of the workspace to prevent underrides. The dispute proceeded to a hearing before an ALJ. The ALJ rejected Chewy’s defense, concluding that the specific regulation addressed a distinct aspect of the underride problem, and did not encompass the ways in which the physical workspace created risk of underrides. Secretary v. Chewey, Inc., OSHRC Docket No. 19-0868, 2022 WL 1009607 (February 22, 2022). The Eleventh Circuit panel took the opposite view.
This blogpost discusses the Eleventh Circuit’s opinion and argues that the result is deeply disturbing.
I. BACKGROUND
A. Reducing Industrial Accidents
Industrial accidents have long caused carnage in the United States.[2] Generally employers can enhance their employees’ safety in two distinct non-exclusive ways. First, the employer can alter the activity or physical surroundings to reduce the dangers to employees. Second, the employer can provide warnings and training that enable employees to reduce or eliminate the risk of injury to themselves or their co-workers.[3] The second almost invariably entails far less expense than the first. But given human frailty, the second will often produce sub-optimal results.[4] It is unreasonable to expect human beings to be absolutely or even reasonably careful 100% of the time.[5]
Moreover, workers, unlike others endangered by the risk-producing conduct, such as consumers, lack full autonomy. Employers can demand that their employees confront dangers at the risk of losing their jobs. Indeed, this is presumably one of the “market failures” that provide a significant justification for OSHA regulation. In effect, OSHA establishes minimum safety standards for workers who cannot afford to leave jobs that confront them with unreasonably unsafe conditions. The existence of workers’ compensation systems, while generally salutary, limits employers’ safety incentives by removing the risk of full tort damages for workers’ injuries. Employers will often bear costs that are far less than the loss their workers suffer by injury or death. This is the trade-off underlying workers compensation insurance.[6]
In addition, some hazards arise out of a variety of workplace setting too sui generis to permit the crafting of a precise rule that will address whether and what methods need be taken to avoid harm.[7] The problem dangers caused by the myriad worksites in which powered industrial trucks operate, and more particularly the dangers of underrides, may present such a situation.[8] It may be difficult, if not impossible, to craft an optimal precise safety rule to address the risk in even a large category of circumstances. At least OSHA appears to have so concluded.[9] Thus, a general requirement of reasonableness, similar to that predominant in tort law with regard to accidental injuries, may be warranted.[10]
B. The Accidents at Chewy’s Ocala Warehouse
The two accidents that precipitated the citation to Chewy occurred in the company’s Ocala, Florida warehouse during 2018.[11] The aisles in the section of the warehouse in which the accident occurred were 127 inches wide, bordered by rack systems on either side. Considering the 102-inch-length of the forklift itself, this left at most a mere 25 inches of clearance before the back end of the forklift’s power section would begin to underride the shelving on the opposite side of the aisle. With this margin of error, the forklift operator would have to pull a pallet clear from the shelving on one side of the aisle and rotate the forklift 90 degrees to travel along the aisle.[12] Apparently, Chewy had experienced underrides that had not resulted in injuries. At least some had occurred because the forklift “had slipped on water” and “slid” underneath shelving.[13]
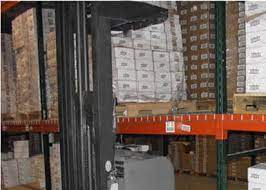
The first of two underride accidents, the non-fatal one, occurred because the forklift operator’s radio wire became entangled with the forklift’s joy-stick control. After an investigation of the accident, the Ocala warehouse’s Safety Manager recommended “lowering the bottom shelf of the racking system so that the [forklift] would hit a cross-beam of the racking system and thus stop the forklift from going under it.” Chewy’s Vice President rejected the proposal because, as the warehouse safety officer would later explain, “the feeling was that if we lowered the load beams . . . , that that would somehow affect the [storage] capacity that we had.”[14] Chewy officials decided, instead, to send workers an advisory on proper headset radio wearing and “change[]” the [forklift] training program. The training regimen was modified to ensure that operators understood the potential hazards associated with underrides. Chewy officials also conferred with the manufacturer of the forklift to add one or two aftermarket posts to the back of the forklift so that contact between the post and the shelving would stop the forklift from underriding shelves and thus protect the forklift operator. The manufacturer refused to approve the request.[15]
The cause of the second, and fatal, underride incident could not be determined, and the Warehouse Safety Manager’s review of the available evidence, including tapes from a camera covering the area in which the accident occured, did not reveal any specific operator error (other than the operator’s failure to swivel his head 90 degrees to look in the direction of travel, namely backward).[16]
OSHA Compliance Safety & Health Officer (“CSHO”) Gerard Driscoll conducted an inspection in response to the fatal accident. As part of that inspection, he referred to OSHA’s published guidance on under-ride hazards, namely its Safety and Health Information Bulletin (SHIB) entitled, “Stand-up Forklift Under-ride Hazards,” published July 29, 2009. The SHIB references the American National Standard ANSI B56.1-2005, which lists “feasible means to abate the under-ride hazard in warehouse environments,” including “lowering the horizontal storage beam to prevent roll-unders.” CSHO Driscoll also noted that the manufacturer’s brochure for the forklift warned that “in some environments of use, the first level horizontal rack beams are higher than the top of the forklift power section and lower than the overhead guard[,] creating “the potential” for “the power section to under ride the rack beam.”
Within two days of the fatal accident, Chewy had lowered the shelving to prevent underrides. Driscoll concluded that Chewy’s lowering of the shelving resolved the underride problem, making it unnecessary to consider other means for ameliorating the underride risk, such as widening the aisles.
After Chewy lowered the horizontal beam at all its warehouses, there was an increase in forklifts striking the lowered beam because, in the words of the Warehouse Safety Manager, the “the aisles were pretty tight.”[17] This suggests the likelihood of frequent underrides, despite the training given operators regarding the danger of underrides, had the shelves not been lowered.
C. The General “Reasonableness” Standard, OSHA’s Powered Truck Regulation, and Preemption
The Occupational Health and Safety Act imposes upon employers a “general duty,” to provide employees “a place of employment which [is] free from recognized hazards that are causing or are likely to cause death or serious physical harm,” 29 U.S.C. § 654(a)(1); see, Chewy, slip op. at 5. As refined by OSHA, and referenced as the general reasonableness principle, to establish a violation of this duty OSHA must establish that:
- a condition or activity in the workplace presented a hazard;
- the employer or its industry recognized the hazard;
- the hazard was causing or likely to cause death or serious physical harm;
- a feasible and effective means existed to eliminate or materially reduce the hazard; and
- the employer knew or, with the exercise of reasonable diligence, could have known that the hazardous condition existed at its worksite.[18]
OSHA has promulgated a safety standard that addresses “safety requirements relating to fire protection, design, maintenance, and use” of “[p]owered industrial trucks,” 29 C.F.R. § 1910.178, of which forklifts are a major subset. 29 C.F.R. § 1910.178(a)(1). The extensive regulations govern many aspects of the use of powered industrial trucks, but none come close to prescribing the design of workplaces to eliminate underride hazards. Indeed, 11 years after promulgating Powered Industrial Truck Operator Training Rule, OSHA published the above-referenced SHIB specifically suggesting potential modifications in warehouse work environments to reduce or eliminate the risk of underrides.
OSHA’s preemption regulation, 29 C.F.R. 1910.5(f), provides that “[a]n employer who is in compliance with any” specific safety standard “shall be deemed to be in compliance with” the general-duty clause, “but only to the extent of the condition, practice, means, method, operation, or process covered by the standard.”
D. The ALJ’s Decision
The ALJ upheld the citation in a lengthy and detailed opinion extensively canvassing the evidence presented at the hearing. First, the ALJ rejected Chewy’s argument that the training standard preempted the general obligation to take reasonable precautions to protect worker safety. In particular, ALJ Baumerich explained:
The particular hazard in this case is the instance when the forklift travels beneath (i.e., under-rides) a horizontal rack beam and the worker is unprotected from that beam striking him/her as the forklift travels beneath it. Respondent argues that the training standards at section 1910.178 — requiring operators to “look in the direction of travel,” and “maintain control” of the forklift — specifically address this particular hazard. To the contrary, these training standards do NOT address what happens in the event of an under-ride. Instead, the training standards are geared toward preventing the under-ride; but as the facts of this case show, under-rides occur despite operator training.[19]
The ALJ found persuasive the analysis of the underride problem in another Occupational Safety and Health Review Commission decision addressing the risk of inadvertent underrides, Secretary v. Pharmasol Co., 2018 WL 5013447 (Sept. 4, 2018).[20] There, the preemption defense was rejected because even when an employer adhered to section 1910.178, “the under-ride hazard would [remain] due to [operator] inattention and inadvertence.”[21] ALJ Baumerich ended her discussion of the preemption issue by noting the testimony of expert witness Guy Snowdy. In particular, she emphasized that he had testified that training alone will not fully protect an operator from the underride hazard, because operators cannot be trained to never lose attention or to always operate perfectly. (Snowdy is the director of training and development, and owner, of MHS Training Corporation, which provides training on lifts and material handling equipment to manufacturers, distributors, and construction companies.)
Under the general duty standard, the ALJ made the requisite findings of liability:
- the existence of an underride hazard within the Ocala warehouse at the time of the two accidents,
- employer and industry recognition of the underride hazard,
- the likelihood that underride hazard at Chewy’s warehouse would cause death or serious harm, and
- that Chewy’s measures for addressing the hazard — extra wide aisles[22] and training — were inadequate, and that lowering the shelving was a physically and economically feasible means of eliminating the hazarded.
With respect to the inadequacy of Chewy’s measures, the ALJ noted that “the training and the aisle width are geared toward preventing an under-ride from occurring [—] [b]ut the facts here show that Chewy experienced “a number” of under-rides despite training and the width of the aisles.”[23]
The ALJ also rejected Chewy’s “unpreventable employee misconduct defense.” It found persuasive the Secretary’s argument “that the training rules Chewy had did not address the underride hazard in this case” because “a well-trained operator driving at a reasonable speed and looking in the direction of travel may — in a moment of inattention or distraction — under-ride a horizontal beam of a shelving unit.”
The ALJ noted that he accorded great weight to expert witness Guy Snowdy’s, testimony that under-ride hazards can be completely eliminated through engineering controls.[24]
E. The Eleventh Circuit Panel’s Decision
The Eleventh Circuit found, contrary to a Department of Labor ALJ, that the specific standard, dealing exclusively with training regarding the operation of forklifts to avoid a number of hazards, including underrides, preempted the defendant employer’s general safety obligation.
The Eleventh Circuit panel noted that OSHA had long maintained that section 1910.178 requires employers to address the underride hazard, and that operator training must encompass such hazards. Chief Judge William H. Pryor, Jr. cited, among other things, the preamble to the 1998 Powered Industrial Truck Operator Training rule,[25] portions of the 2009 SHIB (which discussed training as well as means to alter the workplace to reduce or eliminate the underride hazard), and the Department of Labor’s Pharmacol decision.

The panel found the Secretary’s interpretation of the preemption regulation unreasonable. And, it explained, even assuming arguendo that interpretation were correct, the Secretary had acted arbitrarily and capriciously in applying it. To the panel, the crux of the case was whether the remedies OSHA believed required under the general duty clause could be distinguished from the training approach mandated by OSHA’s powered industrial truck rule. If not, the former could not be viewed as distinct from, and beyond the scope of, the latter.
Judge Pryor explained that the panel could not accept the distinction the Secretary offered between a standard that prevents the under-ride hazard and a standard that addresses the hazards that arise in the event of an under-ride. Accepting that distinction and permitting OSHA to extend it to other cases “would upend the regulatory scheme.” The Secretary could avoid preemption of any standard, and rely on the general-duty obligation, by “distinguishing between the hazards the standard addresses and the hazards that occur when the standard fails.” Instead, Judge Pryor suggested, if a safety standard is failing, the Secretary should modify the standard, by way of public notice and comment rulemaking. Indeed, echoing the amicus brief of the Retail Litigation Center, notice and comment rulemaking would “provide[] the Secretary with critical input from interested parties about the ‘feasibility, potential risk reduction, and/or unintended impacts’ of proposed standard revisions.”[26] In effect, the panel sought to preclude the Secretary from “updating specific safety standards without the required procedural safeguards.”
The ALJ’s interpretation of the preemption regulation was also flawed because in her view compliance with the specific standard must eliminate the hazard in order to preempt the general-duty standard’s application. But, Judge Pryor asserted, nowhere does section 1910.5(f) “require[] that compliance with the standard ‘eliminate’ a hazardous condition.”[27] “And neither the Secretary nor the administrative law judge ha[d] explained why [the Court] should insert that requirement into the test for preemption.”[28]
Moreover, Judge Pryor explained, even assuming arguendo that a standard that prevents an underride should be treated differently from the hazards that arise in the event of an underride, the ALJ had misapplied that test. Both the remedies suggested by OSHA under the general-duty rule and the training rule were designed to prevent underrides. In particular, Judge Pryor noted, the Secretary contended that Chewy was required to either install a metal structure behind a driver that would block an under-ride or modify shelves so that forklifts’ power sections would crash into shelving before before passing under them. Id. But, he explained, “[t]hese measures, like the operator training section 1910.178(l) requires, do not protect a worker in the event of an under-ride.” Instead, again like the training measures, the additional methods were designed to prevent under-rides.[29]
II. OBSERVATIONS
The Eleventh Circuit panel’s ruling is highly questionable and fails to accord appropriate deference to OSHA in interpreting the scope of its specific regulation and its interrelationship to the general obligation to create a safe work environment.
Safety rules may differ in the hazard they address, or they may differ in terms of methodology for reducing risk. With respect to the latter, safety rules may focus on either the physical aspects of the workplace, or enhancing employees’ expertise and carefulness. (Or, of course, they may focus of both.) A rule governing solely the latter, by requiring training, should ordinarily not be viewed as preempting the general burden on employers of enhancing safety if that general burden is used to find the employer liable with respect to the physical risk-creating aspects of the workplace. Indeed, when changing the environment to reduce the risk of injury is physically and economically feasible, warnings and training should almost never be viewed as a substitute for altering the work environment.[30] At least such a position should not be taken unless OSHA has specifically indicated that it has adopted such an approach.
To state it differently, the fundamental distinction between the two types of remedies is the assumption of unfailing operator attention. The training precaution presumes that workers will never suffer moments of inattention. If they do, their training becomes irrelevant in terms of accident prevention, at least during the period of the lapse. Precautions involving physical changes to the workplace or to the forklift itself are not premised on constant operator attention – even when an operator is momentarily inattentive the precaution eliminates or minimizes the risk of accidents. This is a fundament distinction and reflects a judgment that avoidance of workplace injuries should not solely be the responsibility of forklift operators. At hearing,CDHO Driscoll would testify that “all the training in the world isn’t going to prevent you driving your forklift under a shelf.” Expert witness Guy Snowdy emphasized precisely the same point.[31]
Note that Chewy’s management did not adhere to industry standards involving the height of shelving, an industry standard designed to prevent underrides. Nor did the management heed the forklift manufacturer’s advice with regard to the height of shelving. Training should not absolve Chewy from failing to meet industry standards for safety and the forklift manufacturer’s advice in order to maximize the storage space at Chewy’s warehouse.
Indeed, the Eleventh Circuit panel’s decision suggests that even now Chewy can abandon the remedial measure it adopted following the fatal accident and return to placing the cross-beams at a height such that the operator’s body contacts the cross-beam before any part of the forklift. As long as Chewy makes sure to cover the risk during operator training, it could avoid any sanction from OSHA no matter how many unnecessary deaths and injuries occur.
To be sure agencies hesitate to pursue a notice-and-comment process to update regulations. Such notice-and-comment processes can consume enormous resources. And agencies may at time abuse their power to issue guidance, as some have feared. But these concerns should not require agencies to promulgate rules, rather than issuing guidance and deciding matters on a case-by-case basis, when the issue is most appropriately addressed using a case-by-case application of a reasonableness principle due to the enormous variation of multifaceted circumstances in which underride hazards are present.
The ALJ can be faulted for the precise manner in which she articulated the distinction between the specific training rule and the general reasonableness rule. And the Eleventh Circuit panel displayed great virtuosity in effectively picking apart the ALJ’s characterization of the distinction between training and raising the height of the shelving. But the essence of the distinction the ALJ drew was easy to follow – namely that rules that cover merely training do not ordinarily preempt any general to modify the physical setting to eliminate, or at least reduce, the hazard about which the employee is being trained. That reasoning provides an ample basis for upholding the ALJ’s, and the Secretary’s, determination in the Chewy case.
III. CONCLUSION
I conclude this blogpost with a vignette. A faculty member at a local college complained that an emergency telephone on the campus was dead and could not be used to summon help. A week later, the college’s maintenance department reported that it had “resolved” the problem. Delighted, and a bit surprised given his experience with maintenance department delays in effecting repairs, the professor went to see for himself whether the phone really worked. He discovered that an “Out of Order” sign had been placed on the phone. In effect the maintenance department had addressed a hazard by alerting the community to the danger of relying on the emergency phone, rather than by eliminating an entirely unnecessary risk (by actually repairing the broken emergency phone).
This is exactly the approach the Eleventh Circuit panel imposed upon OSHA, when it interpreted the OSHA rule regarding industrial truck operator training as preempting the general duty to eliminate remediable hazards well known in the warehousing industry, by virtue of (1) industry-wide standards, (2) warnings by the manufacturers of forklifts, and (3) guidance produced by OSHA itself directly addressing the problem of underrides. The implications of this expansive interpretation of the scope of specific safety rules directed at training, along with the panel’s apparent failure to appreciate the need for case-by-case application of safety standards in some contexts, are quite disturbing.
Let us see if the Government seeks certiorari for review of the decision. Of course, the Government may be hesitant, for fear that this decision reflects the current mood at the Supreme Court.
[1] Guy Snowdy, Identification and The Prevention Of Under-Ride Hazards (April 2020)(asserting that the underride hazard “has been recognized for many years by OSHA, ANSI/ITSDF and other industry organizations and manufacturers for more than 30 years,” and noting “a spike over the past several years of accidents associated with this hazard, many of which are resulting in fatalities”).
[2] Judson McLaury, The Job Safety Law of 1970: Its Passage Was Perilous (originally published in in the Monthly Labor Review (U.S. Bureau of Labor Statistics March 1981); see generally, JOHN FABIAN WITT, THE ACCIDENTAL REPUBLIC: CRIPPLED WORKINGMEN, DESTITUTE WIDOWS, AND THE REMAKING OF AMERICAN LAW 22-42 (2004); OSHA at 30: Three Decades of Progress in Occupational Safety and Health.
[3] I explore this distinction in Bernard W. Bell, Unnecessary Dangers and Acceptance of Risk (unpublished manuscript available on SSRN).
Professor Mark Grady has discussed the distinction in terms of “durable” and “non-durable” precautions. Durable precautions are ones that do not rely on human memory. Non-durable precautions rely on human memory. To illustrate, Grady references the innovation of using magnets on refrigerator doors. Children would often get locked inside discarded refrigerators when people forgot to take the removed refrigerator doors before discarding them. Use of magnets obviated the need for reliance on refrigerator owner’s memory. Mark Grady, Why Are People Negligent? Technology, Nondurable Precautions, and the Medical Malpractice Explosion, 82 NW. U. L. REV. 293, 295, 297, 299-300 (1988).
[4] See, e.g., Howard Latin, Good Warnings, Bad Products, and Cognitive Limitations, 41 UCLA L. REV. 1195, 1193-1198 (1994). The field of human factors engineering, described here and here, considers the ways in which human failings interact with technology in ways that may exacerbate risk.
[5] RESTATEMENT (THIRD) OF TORTS: LIABILITY FOR PHYSICAL AND EMOTIONAL HARM §3, comm. k (“[b]ecause the jury focuses on the conduct of the reasonably careful person in each particular case, the fallibility of average persons over a period of time is a reality the jury is not in a position to consider”); Why Are People Negligent?, supra, 82 NW. U. L. REV. at 303; see, Ga. Elec. Co. v. Marshall, 595 F.2d 309, 321 (5th Cir. 1979) (upholding OSHA citation because even though the machine’s operator knew about the mislabeling of the machine’s controls and “ordinarily compensated for it,” the “hazard was nonetheless present because a momentary lapse in concentration . . . could have resulted in . . . very serious consequences”).
[6] For extensive discussion of the market imperfections in the worker safety context, see OSHA, U.S. DEP’T OF LABOR, FINAL ECONOMIC ANALYSIS AND FINAL REGULATORY FLEXIBILITY ANALYSIS. SUPPORTING DOCUMENT FOR THE FINAL RULE FOR OCCUPATIONAL EXPOSURE TO RESPIRABLE CRYSTALLINE SILICA, Chapter II: Market Failure and the Need for Regulation (March 24, 2016). For extensive discussion of the interrelationship of the labor market, workers’ compensation, tort compensation, and OSHA regulation, see Sidney A. Shapiro, Occupational Safety and Health Regulation, ENCYCLOPEDIA OF LAW AND ECONOMICS (Boudewijn Bouckaert & Gerrit De Geest eds. 2000).
[7] This was recognized in Chenery v. SEC, 332 U.S. 194 (1947), where the Supreme Court explained that one reason an agency can legitimately decide to proceed by case-by-case adjudication rather than rulemaking is that “the [regulatory] problem may be so specialized and varying in nature as to be impossible of capture within the boundaries of a general rule.” Id. at 202-203. In those situations, it noted, “the agency must retain power to deal with the problems on a case-to-case basis if the administrative process is to be effective.” Id. at 203.
Indeed, much of the law of unintentional torts is premised on this basis, including the principle that compliance with safety statutes does not serve to preclude a finding that an actor has acted negligently. In other words, a specific safety regulation does not override an actor’s general tort “duty of care.” See note 10, infra.
[8] As OSHA noted in a 1998 rulemaking:
The workplaces where these trucks are being used . . . present a variety of different hazards. The safety of industrial truck operations can be decreased by workplace conditions such as rough, uneven, or sloped surfaces; unusual loads; hazardous areas; narrow aisles, blind spots, or intersections; and pedestrian traffic or employees working close to the path of travel.
OSHA, Final Rule, Powered Industrial Truck Operator Training, 63 Fed. Reg. 66238, 66243 (1998) (emphasis added). Indeed, the differing dangers were so multifaceted that even a training program had to include not just the general hazards of workplaces attendant operation of a powered industrial truck, but also “the hazards of the particular workplace where the vehicle operates.” Id.
[9] See, id.
[10] Not only is the law of personal injury dominated by the amorphous reasonable person standard, but compliance with applicable statutes ordinarily does not preclude a finding of negligence, i.e., the failure to exercise due care, reflected in the general negligence standard. RESTATEMENT (THIRD) OF TORTS: LIABILITY FOR PHYSICAL AND EMOTIONAL HARM, supra, at §16(a).
Granted, in some situations a court can conclude that compliance is sufficient to establish “due care” “[w]hen the statute directly addresses the particular safety problem before the court, [and] evidently seeks to identify all the precautions called for by the general negligence standards . . ., and when the particular case involves no unusual circumstances.” Even then a court must consider “the evident thoroughness of the statute and the desirability of a uniform liability standard that can simplify litigation and provide parties with appropriate guidance as to what precautions are expected of them.” See generally, Theresa Moran Schwartz, The Role of Federal Safety Regulations in Products Liability Actions, 41 VAND. L. REV. 1121 (1988).
One of the reasons courts, either in the torts or administrative law contexts, might doubt the sufficiency of a standard of conduct is the time it takes an agency to create or modify the applicable standard. For a criticism of OSHA on this score, albeit dated, see U.S. Government Accountability Office, Multiple Challenges Lengthen OSHA’s Standard Setting, GAO-12-330 (April 2012); see generally, RACHEL AUGUSTINE POTTER, BENDING THE RULE: PROCEDURAL POLITICKING IN THE BUREAUCRACY 131-32 (2019).
[11] The warehouse had been opened in 2017, no more than 18 months before the first accident. Secretary v. Chewey, supra, 2022 WL 1009607 at *2.
[12] ALJ Opin., at *3.
[13] Id. at 10.
[14] Id. at 7.
[15] Id. OSHA regulations provide that companies may not make post-sale “modifications and additions which affect . . . safe operation . . . without [the] manufacturer[‘]s prior written approval.” 29 C.F.R. §1910.178(a)(4). Many products liability cases arise from post-sale modifications of industrial equipment by employers. See, e.g., Jones v. Ryobi, 37 F.3d 423 (8th Cir. 1994); Robinson v. Reed-Prentice Division, 403 N.E.2d 440 (1980); see generally, DAVID G. OWENS, PRODUCTS LIABILITY LAW §12.3 at 782-84.
[16] Because the forklift operator stands perpendicular to the direction of travel, the operator could look “backward” by merely swiveling his/her head.
[17] Id. at *12.
[18] Chewy, supra, slip op at 5; Ga. Elec. Co. v. Marshall, 595 F.2d 309, 320–21 (5th Cir. 1979)(cited in Chewy); Arcadian Corp., 20 BNA OSHC 2001, 2007 (2004); Tampa Shipyards, Inc., 15 BNA OSHC 1533, 1537 (1992).
[19] ALJ Opin. at *20 (emphasis added).
[20] The ALJ noted that training standards, by definition, cannot address the problem of inadvertent underrides. Id. at *22.
[21] Pharmasol, supra, 2018 WL 5013447, at *6.
[22] This reference is a bit odd because even though Chewy suggested at the hearing that it had extra-wide aisles, the warehouse manager testified that the aisles in the Ocala warehouse were tight, and Chewy did not widen its aisles in response to either accident. ALJ Opin. at *13.
[23] Id. at 28.
[24] The ALJ also observed:
“Here, the record shows that instances of a wet floor, a radio cord, and an as yet unknown reason, caused a Chewy worker to lose control of his forklift, and then subsequently under-ride a rack beam in a Chewy warehouse. Mr. BB was seriously injured, and Mr. RP died, because of those incidents. The training and the width of Chewy’s aisles did not address the under-ride hazard in those instances.”
Id. at *29.
[25] The Court noted that the preamble to the Notice of Final Rule setting out the Powered Truck Operator Training Rule noted the dangers of a forklift operator driving into a column — [t]his standard addresses the Secretary’s concerns about the risk that a forklift could “run into a column or other part of the building.” Slip op. at 6 (citing the preamble to the Powered Industrial Truck Operator Training Rule, 63 Fed. Reg. 66238, 66243 (1998)). But the preamble makes this observation with regard to the risks of “operating a powered industrial truck at excessive speed or in conditions of restricted vision in the line of travel due to the load being carried.” And again, the comment was made with regard to alerting operators to the hazards, not with regard to the feasibility of eliminating the hazards themselves in some circumstances by modifying the workspace. The passage certainly does not suggest that employers need not eliminate unnecessary hazards.
In addition, driving into “a column” will likely not result in the same type of crushing injuries that result from underrides. In an impact with a column, either the load being transported (if it extends beyond the forklift) or the forklift itself will bear the brunt of the impact. This is particularly true in the context in which OSHA discussed the problem, obscured vision due to the size of the load being transported. But it is even true when the forklift is moving “backward,” and, thus, the operator’s vision is not obscured by the load. The lower portion of the forklift, i.e., the forklift’s power section, will first come into contact with a vertical column. However, when there is a poorly placed horizontal cross-beam, the operator’s body can hit the cross-beam before any part of the forklift does.
[26] The amicus brief is available on westlaw. Brief of Amicus Curiae Retail Litigation Center, Inc. in Support of Petitioner and Reversal, Chewy v. U.S. Dep’t of Labor, No. 22-11626, 2022 WL 11900603 (September 8, 2022).
[27] Slip. op. at 9. This, of course, is hardly surprising. Some hazards cannot be fully eliminated, for example hazards due to the presence of toxins in the environment. Others perhaps can be eliminated. If a hazard can be eliminated, in at least some workplaces at reasonable cost, it is not clear why it should not be. Cf., Adams v. Bullock, 227 N.Y. 208, 211, 125 N.E. 93 (1919)(Cardozo, J.)(“chance of harm, though remote, may betoken negligence, if needless[;] [f]acility of protection may impose a duty to protect”). The Eleventh Circuit panel did not attempt to explain why employers should be under no obligation to eliminate preventable hazards.
[28] Id.
[29] Judge Hall, in a separate concurrence elaborated upon the themes in Judge Pryor’s opinion for the panel.
[30] See Unnecessary Dangers and Acceptance of Risk, supra.
[31] ALJ Opin. at 22 (citing the testimony of CSHO Discoll and expert witness Snowdy).